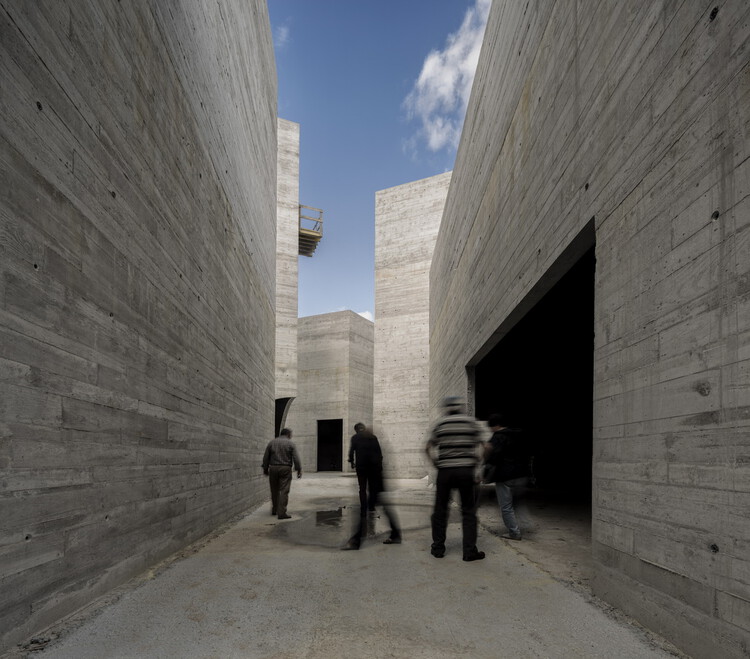
“Se a indústria do cimento fosse um país, seria o terceiro maior emissor de dióxido de carbono do mundo, com cerca 2,8 bilhões de toneladas, superado apenas por China e Estados Unidos.” Essa afirmação chama muita atenção na reportagem de Lucy Rodgers para a BBC, sobre a pegada ecológica do concreto. Com mais de 4 bilhões de toneladas produzidas por ano, o cimento responde por cerca de 8 por cento das emissões globais de CO2 e é elemento fundamental para a produção de concreto, o produto mais fabricado no mundo. Para se ter uma noção, produz-se cerca de meia tonelada de cimento por pessoa do mundo todo ano, o suficiente para construir 11.000 edifícios Empire State. Com esses números impressionantes, há alguma forma de reduzir este impacto?
Para a fabricação de cimento, calcário, argila e areia são aquecidos em fornos super quentes, que chegam a 1450° C. Isso forma o clínquer, que depois é misturado com gipsita (gesso) e outros aditivos como pozolana, calcário e outros. O cimento corresponde a cerca de 10% da mistura do concreto. Os outros componentes básicos são areia, brita (agregado graúdo e miúdo) e água. Na produção de cimento há dois principais aspectos que resultam em emissões de dióxido de carbono. Segundo este artigo de Robbie M. Andrew, a primeira é a reação química envolvida na produção do principal componente do cimento, o clínquer, à medida que os carbonatos (principalmente CaCO3, encontrados no calcário) são decompostos em óxidos (principalmente cal, CaO) e CO2 pela adição de calor. A segunda fonte de emissões é a utilização de combustíveis fósseis para gerar a energia significativa necessária para aquecer os ingredientes brutos a bem mais de 1000 °C. Ou seja, durante a produção de cimento, são consumidos grandes quantidades de combustíveis (geralmente de fontes não-renováveis, como coque de petróleo, gasolina ou gás natural) e emitidos diferentes gases poluentes, entre eles o monóxido e dióxido de carbono. Segundo este estudo, “a reação química de calcinação é responsável por aproximadamente 52% das emissões de CO2 no processo de fabricação do clínquer, enquanto o consumo de energia responde pelo restante. (...) Considerando o consumo energético, tem-se que a cada 1.000 kg de clínquer fabricados gera-se em média aproximadamente 815 kg de CO2 no processo de fabricação do clínquer.”
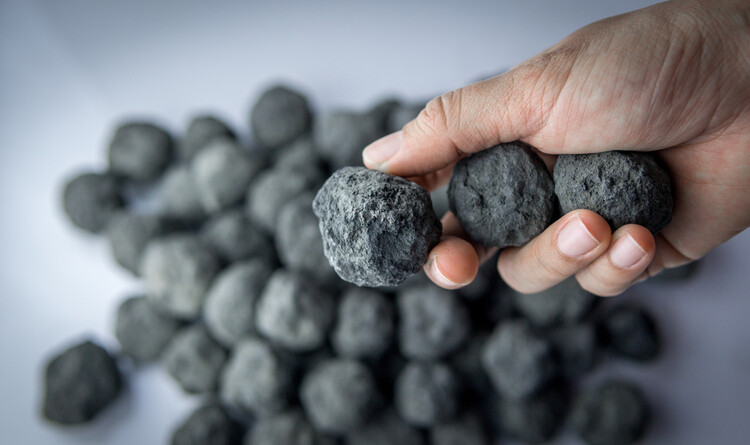
É possível reduzir uma parte desse impacto. Se é na produção do clínquer que a maior parcela das emissões ocorrem, a substituição deste por outros materiais pode fazer uma grande diferença. Os chamados materiais de cimentação suplementares (SCMs) são geralmente subprodutos de outras indústrias, como escória da produção de aço e cobre, areias de fundição de operações de fundição de metal e cinza volante, cinza inferior e gesso sintético de concessionárias de energia elétrica. Ao substituir parte do clínquer por esses materiais, o concreto adquire novas características, que podem ser desejáveis em alguns casos, mas principalmente mostram uma notável capacidade de reduzir a emissão de CO2. Outra possibilidade é a cinza vulcânica, uma alternativa ao cimento já conhecida há milhares de anos, que foi o que permitiu aos gregos e romanos erigirem construções tão resistentes, que permanecem impassíveis desde então. Ao aquecer cal e cinza vulcânica a cerca de 900° C, e depois misturar isso com água do mar, atinge-se um material extremamente resistente e estável.
Mas as inovações podem ir além. CarbonCure, por exemplo, busca reduzir as emissões de dióxido de carbono de uma forma bastante distinta. A startup canadense desenvolveu um processo chamado Mineralização de CO2, que consiste em injetar dióxido de carbono na mistura de concreto, fazendo-o reagir com os íons de cálcio do cimento para formar um mineral de tamanho nanométrico, o Carbonato de Cálcio, que fica embutido no concreto, tornando-o mais resistente.
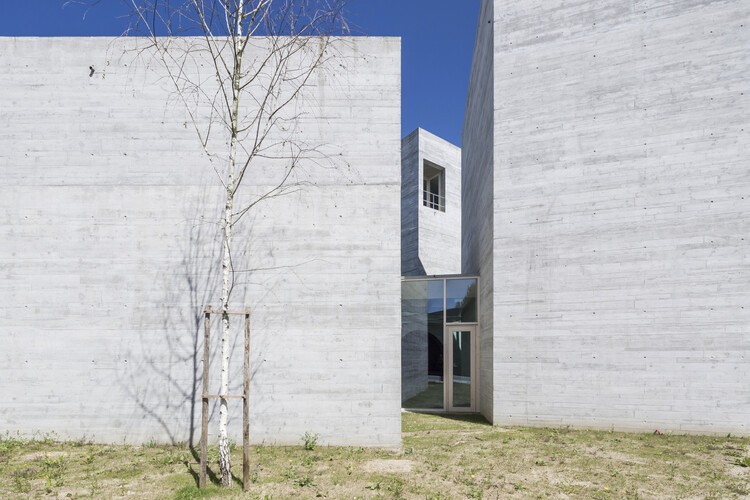
A empresa Solidia Tech tem desenvolvido experimentações em torno de uma nova receita de cimento que substitui o calcário pelo mineral wollastonita, que não elimina o dióxido de carbono. Já que não requer aquecimento. Além disso, ele reteria dióxido de carbono no ar durante a cura, criando um produto com emissões negativas. Como aponta este artigo, o resultado é que os blocos de concreto feitos de cimento da Solidia capturam cerca de 240 kg de dióxido de carbono para cada 1.000 kg de cimento usado na mistura. Isso além de menos emissões produzidas durante a fabricação do cimento.
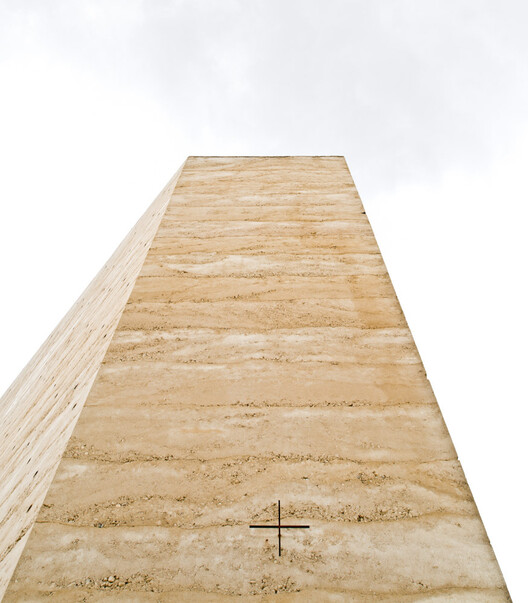
A BioMason é uma startup da Carolina do Norte com uma abordagem distinta, produzindo um concreto sem cimento Portland ou emissão de dióxido de carbono. Em vez de cimento Portland, é utilizado biocemento para unir areia e brita. Através da incorporação de agregados reciclados com micróbios bacilos vivos, isso desencadeira a combinação de carbono com cálcio para criar cristais de calcário, sem a necessidade de aquecimento. Enquanto o concreto tradicional pode levar até 28 dias, o Biomason biocement® atinge sua resistência final em menos de 72 horas de crescimento. O material final consiste em aproximadamente 85% de granito de fontes recicladas e 15% de calcário cultivado biologicamente.
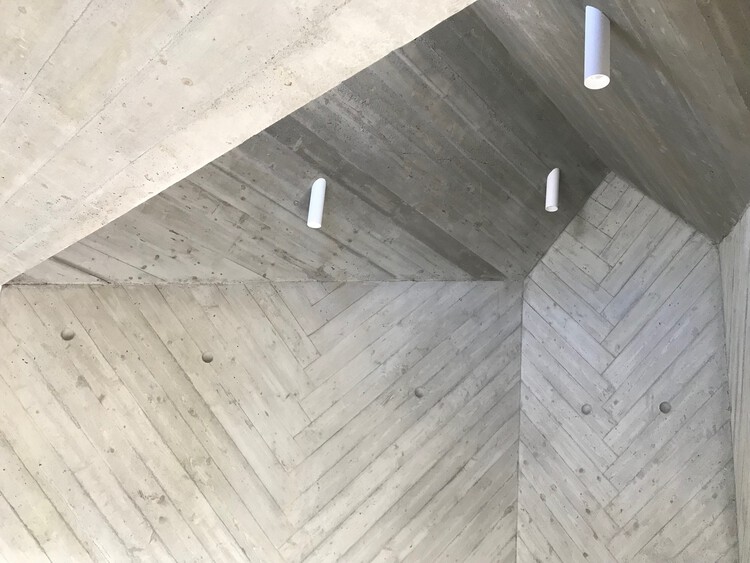
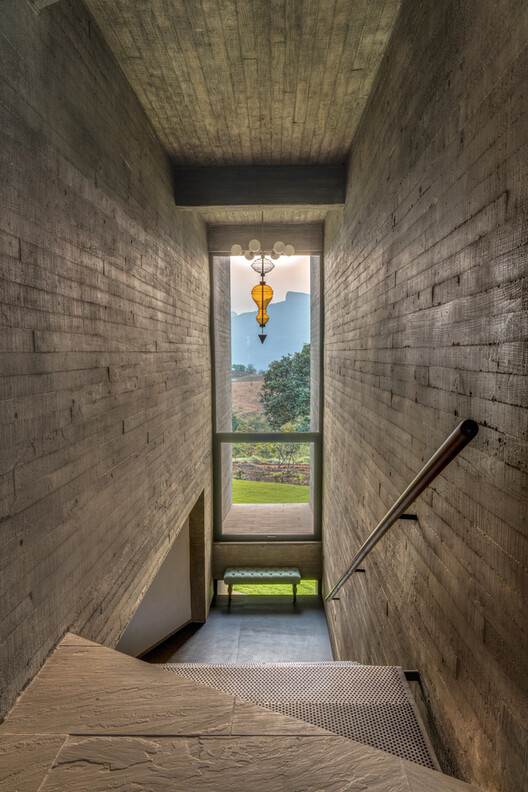
Já Engenheiros da Lancaster University no Reino Unido trabalharam em colaboração com a Cellucomp Ltd UK para estudar os efeitos da adição de “nanoplaquetas” extraídas das fibras de raízes vegetais para melhorar o desempenho das misturas de concreto. As pesquisas têm mostrado que os concretos de compósitos vegetais, feitos de vegetais como beterraba ou cenoura, têm desempenho estrutural e ambientalmente superior a todos os aditivos de cimento disponíveis no mercado, como grafeno e nanotubos de carbono, a um custo muito mais baixo. O potencial dos concretos de compósitos vegetais está na capacidade das nanoplaquetas de aumentar a quantidade de silicato de cálcio hidratado nas misturas de concreto, principal substância que controla o desempenho estrutural. O efeito indireto significa que quantidades menores de concreto seriam necessárias para a construção. As nanoplaquetas podem melhorar a qualidade do produto, reduzindo o número de fissuras que aparecem no concreto, ajudando a prevenir a corrosão e aumentando a vida útil do material. Há muitos outros exemplos de empresas buscando soluções para reduzir as emissões na produção de cimento e concreto, e este artigo de Akshat Rathi abrange boa parte delas, com informações muito valiosas sobre o tema.
A crise climática tem demandado soluções urgentes e, aos poucos, a indústria da construção começa a aceitar mais materiais alternativos que possam contribuir para a mudança. O cimento e o concreto carregam uma enorme importância, que pode se transformar do impacto negativo para melhorias positivas para o meio ambiente. O artigo evidencia que tornar o cimento um material menos poluente é uma tarefa bastante complexa, que envolve muitos recursos e tempo envolvido em pesquisa. Cabe nos perguntar se, no futuro, o concreto deve manter-se o material protagonista da indústria da construção ou se é possível pensar em substituí-lo ou misturá-lo com outros materiais inerentemente menos poluentes